製 品 Product
自動車用鋼管への取り組み
①軽量化、②高剛性化、③コスト削減ニーズに貢献できる自動車部品の鋼管化技術を開発します。
開発方法
- 商品開発(素材開発)と鋼管2次加工、評価・検査技術開発をセットで推進し、鋼板プレス品、棒鋼部品からの鋼管化を支援します。
- 素材開発から実部品試作支援までの一貫体制により自動車部品の鋼管化を推進します。
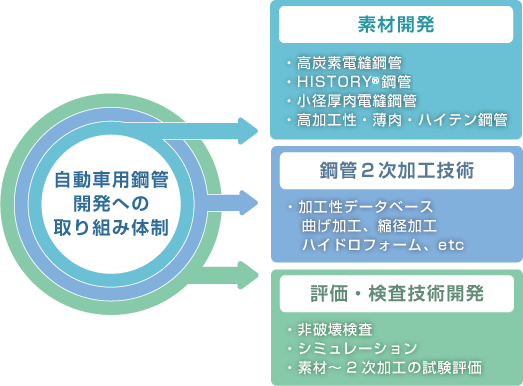
供給能力
- 自動車用鋼管に必要な電縫鋼管(ERW、HISTORY®)と継目無鋼管(SML)の提供が可能です。
Only1 | No.1 |
---|---|
|
|
図2 JFEのOnly1技術とNO.1製品(鋼管)
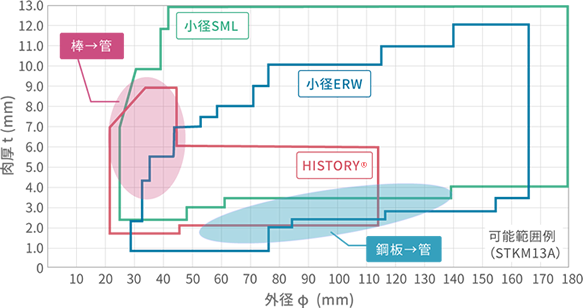
適用可能な自動車部品
スタビライザー、ドライブシャフト、フロントピラー補強材、トーションビーム、トレーリングアーム、ロアアーム、ラックバー、サブフレーム、ドアインパクトバー、シートフレーム脚、ステアリングシャフト、パワーステアリング、ステアリングハンガービーム、ショックアブソーバー、リアアクスルハウジング、ドラッグリンク、トルクロッド、二輪車用フロントフォークなど
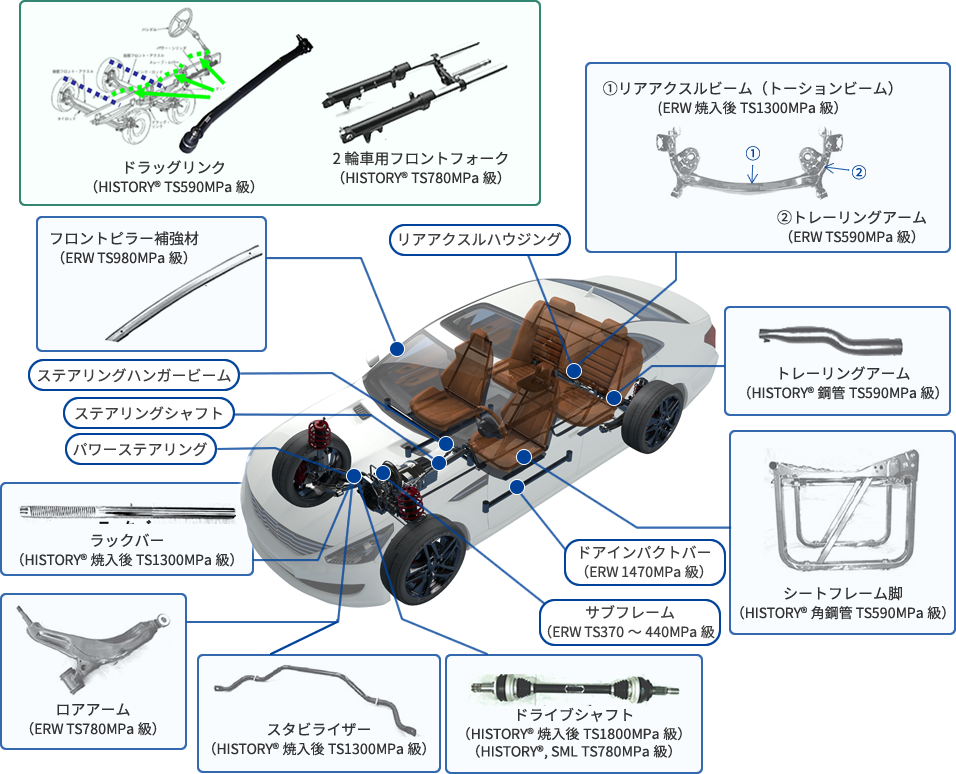
JFEの自動車用鋼管の種類と特長
ドライブシャフト用HISTORY®鋼管
ドライブシャフトの中空化を達成するHISTORY®鋼管
自動車部品の軽量化ニーズに対応した高炭素自動車用鋼管です。細径厚肉への対応が可能なため、従来棒鋼が適用されていた部品を中空化することができます。加工性が良好なため、加工前の焼準が不要で、また、継目無鋼管に比べて高い寸法精度を有しています。
特 長
- 肉厚/外径比30%の細径厚肉鋼管に適応可能です。(図1)
- インライン加熱・圧延で焼準相当の機械的特性が得られます。(表1)
- 継目無鋼管に比べ高い寸法精度が得られます。
- インライン・インダクション加熱による急速加熱で表面の脱炭を抑制しています。(図2)
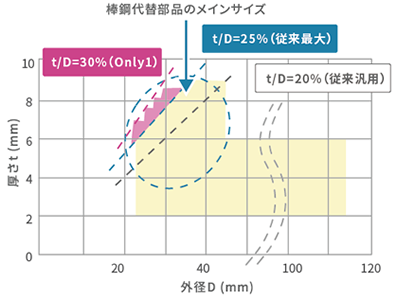
YS(MPa) | TS(MPa) | EL(%) | |
---|---|---|---|
HISTORY®鋼管 | 403 | 674 | 44 |
電縫管 焼準材 |
393 | 672 | 42 |
熱処理をせずに冷間加工(冷牽)が可能です。
表1 引張特性
(素材:S45C,JIS11号試験片)
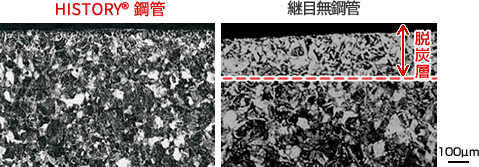
焼入れ後も均一な硬さが得られます。
図2 管外表面の脱炭層比較
(SAE1541 0.42%C)
技術のポイント
- 鋼管製造時の材料の形状や溶接部の形状を監視するモニター、溶接異常を検出するセンサーなどを駆使することで、高品質の高周波電気抵抗溶接鋼管が得られます。
適用例
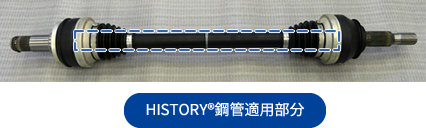
- 焼入れ一体型(MTS):0.35%C-1.5%Mn-B
焼入れ後引張強さ1800MPa級 - 摩擦圧接型(WTS):0.41%C-1.5%Mn
熱処理後引張強さ780MPa級
スタビライザー用HISTORY®鋼管
優れた電縫溶接部特性と加工性を有するスタビライザー用HISTORY®鋼管
温間縮径圧延により電縫溶接部の焼入れ硬化を解消し、母材と同等の特性を実現しているため、均質で高い加工性を有する高炭素自動車用鋼管です。また、細径厚肉への対応が可能なため、従来棒鋼が適用されていた部品を中空化することができます。
化学成分と製造可能範囲
- 必要強度によって各種グレードの材料が製造可能です。 (表1)
- 細径厚肉への対応が可能です。(図1)
JFE独自規格 | 相当規格 | 化学成分(mass%) | |||
---|---|---|---|---|---|
C | Si | Mn | その他 | ||
HISTORY22CB | SAE10B23 | 0.23 | 0.2 | 0.6 | Cr, Ti, B |
SAE15B26 (26MnB5) |
0.26 | 0.2 | 1.2 | Cr, Ti, B | |
SAE15B37H (34MnB5) |
0.34 | 0.2 | 1.2 | Cr, Ti, B | |
HITEN490 | SAE15B22 | 0.20 | 0.2 | 1.4 | Cr, Ti, B |
HITEN590 | SAE15B24 | 0.19 | 0.4 | 1.6 | Nb, Ti, B |
表1 スタビライザー用HISTORY®鋼管の化学成分
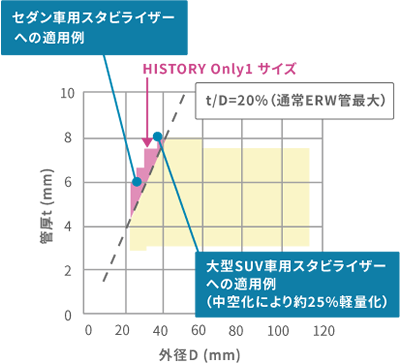
従来のERW管では製造が困難な小径厚肉の電縫管(内面溶接ビード除去)が製造可能で、高い寸法精度が要求される
スタビライザーの中空化(軽量化)に貢献できます。
図1 スタビライザー用HISTORY®鋼管の製造可能範囲
(●は小径厚肉のOnly1サイズでの適用例)
特 長
- 温間縮径圧延技術により、溶接部も含めて均一な硬さ(焼入れ後)を得られます。(図2)
- 加工の際の減肉が少ないため、優れた疲労特性を発揮します。(図3)
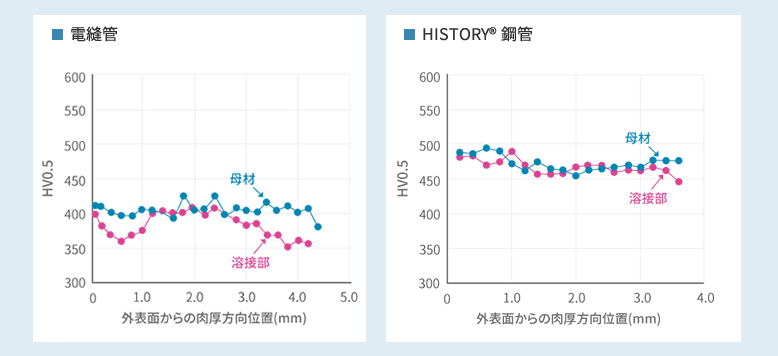
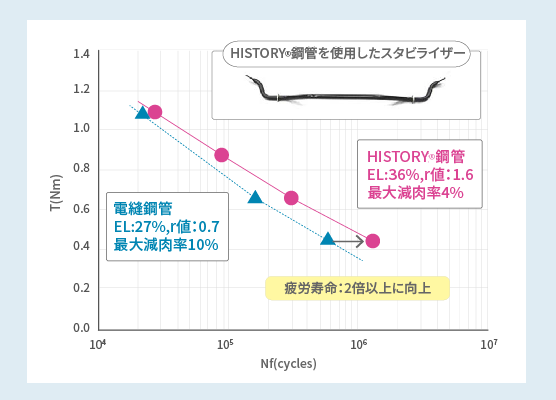
小径厚肉機械構造用鋼管
JFE溶接鋼管株式会社
独自の成形、溶接技術を駆使した高信頼性の小径厚肉電縫鋼管
t/D(肉厚/外径)最大25.7%(27.2×7.0)の小径厚肉鋼管を、独自の特殊な成形技術と健全な溶接部を確保する高い電縫溶接技術で製造し、お客様から高い信頼を得ています。
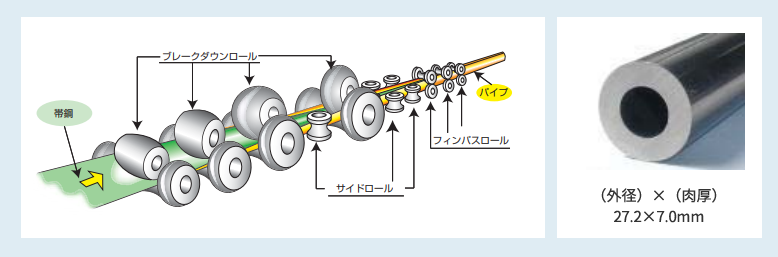
特 徴
- 小径厚肉鋼管
外径10mm~34mmで肉厚最大7.0mmの機械構造用電縫鋼管を製造しています。通常の炭素鋼だけでなく、S45C・SCM材等の高炭素鋼・低合金鋼及び高張力鋼についても製造しております。 - 内面ビード切削
当社独自の内面ビード切削技術を駆使し小径管の内面ビードを除去し、国内では最小内径となる内径8mmまでのビード切削管を製造しています。これにより、部品加工の容易化、伸管回数の低減などを通じてお客様の最終製品のVA提案などに寄与しています。 - 用途と新商品開発
お客様のご指導のもとに当社独自技術で下記の新商品を開発し高い評価を受けています。
・自動車用高圧パワーステアリング配管用素管
・高強度自動車ヘッドレスト用鋼管
・高強度自動車スタビライザー用鋼管
・建機用高圧力油圧配管
・構造用Pipe In Coil鋼管 - 納期・ロット
お客様に最適な製品を提案し、ご要望に応じて、最短3日、最小ロット500kgからお届けします。
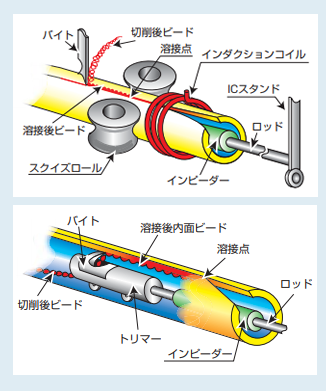
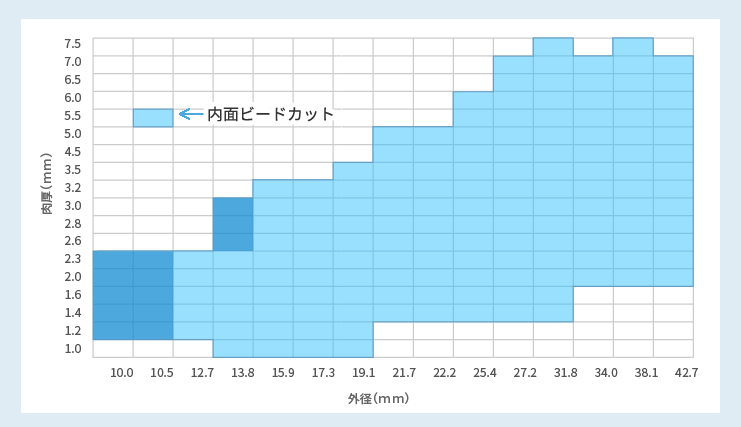
トーションビーム用電縫鋼管
疲労特性・成形性に優れた高剛性パイプトーションビーム用鋼管
自動車部品の軽量化、高剛性化というニーズに対応した、成形性と実用的機能特性に優れた高機能自動車用鋼管です。従来の、U字型に成型加工した鋼板と、棒鋼のスタビライザーを組み合わたリアサスペンションを、単一部品で代替することができ、優れた剛性によって、操縦安定性とより良い乗り心地の両立を可能にします。
特 長
- 相反する「高い疲労強度(図1)」と「成形性(図2)」を両立します。
- 1200MPaを超える高強度を得るための焼入れ性、低温靭性、耐遅れ破壊特性などの実用的機能特性のバランスがとれます。(図3)
- 管内面マーキングにより短管切断後もトレースバックが可能です。
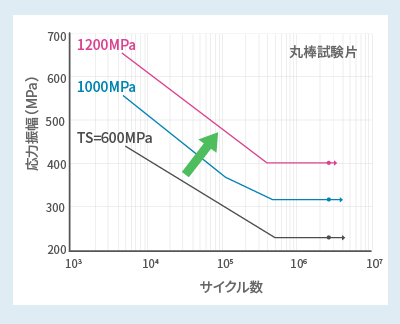
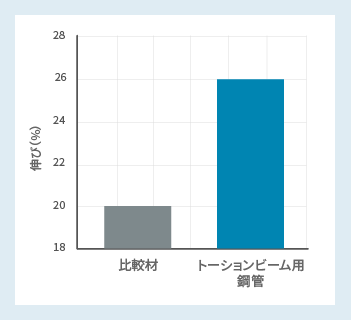
(JIS12号弧状片)
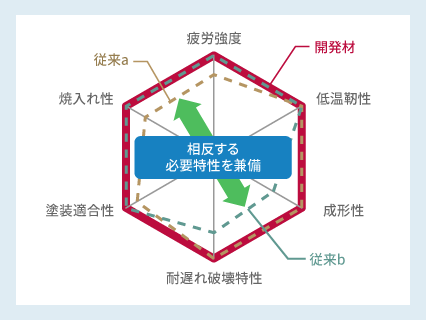
技術のポイント
- 製鋼での炉外精錬による高純度化技術
- 熱間圧延における高精度制御冷却技術
- 鋼管製造での電縫部高精度温度制御技術
↓
これらを駆使して、化学成分とミクロ組織を最適化することにより製造します。
- 独自の成分設計により、お客様の製造工程における焼入れ性を確保します。
適用可能な自動車部品
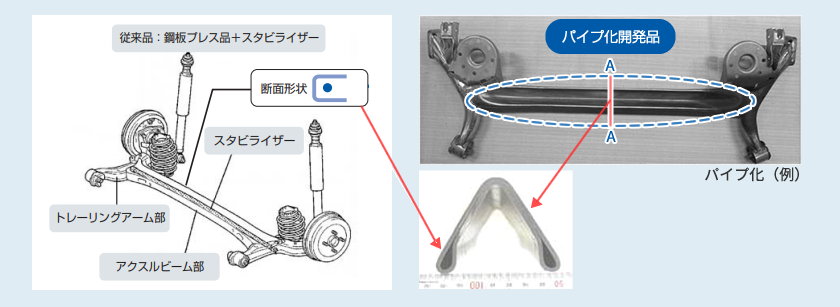
高加工性・薄肉・ハイテン電縫鋼管
複雑形状部品の中空化・高強度化が可能
高い加工性と強度を両立した電縫鋼管です。 延性が良好なため、複雑な形状に加工することが可能で、鋼管特有の閉断面構造を活用して、部品の高剛性化、軽量化が達成できます。また、溶接などの工程の削減にも寄与します。
特 長
- 鋼管の曲げ加工、ハイドロフォーミングなどの2次加工性能に優れたハイテン鋼管を提供できます。(図1、図2)
- 安定した電縫溶接品質の薄肉ハイテン鋼管を提供できます。
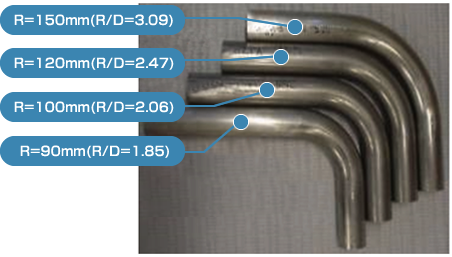
(φ48.6mm×t2.0mm、t/D = 4.1%、回転引き曲げ加工)
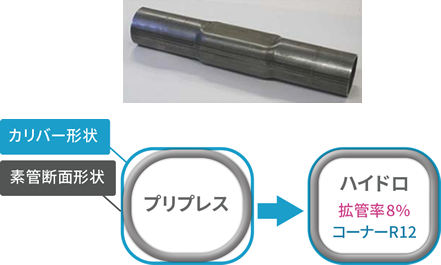
980MPa級電縫鋼管の加工
(φ48.6mm×t2.0mm、t/D = 4.1%)
採用例
- フロントピラー補強材
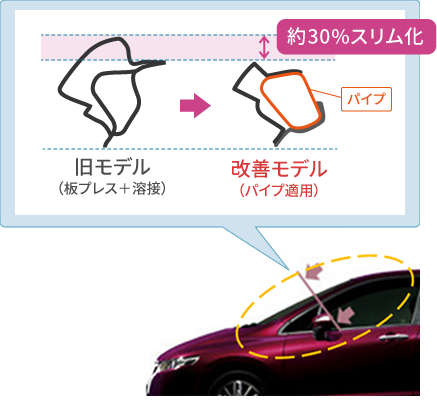
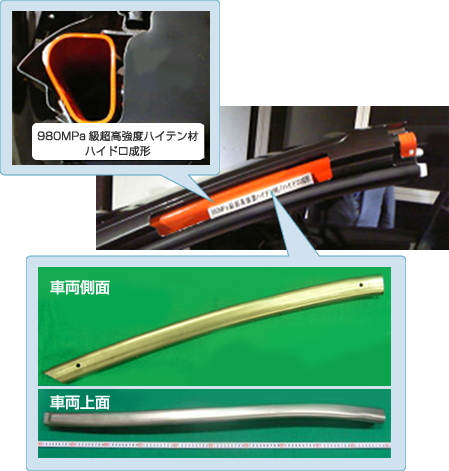
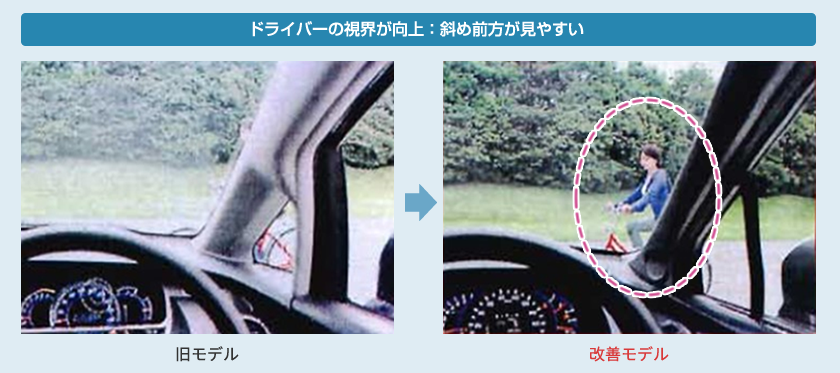
自動車を支える技術
1台の自動車の中には様々な鋼管が使われています。
特にステアリング、足回り、パワートレイン、といった自動車にとって非常に重要な「走り」をコントロールする場所に鋼管は多く使われています。
より安全で快適な「走り」を支える素材として、JFEスチールは自動車用鋼管の開発・技術研究に力を注いでいます。
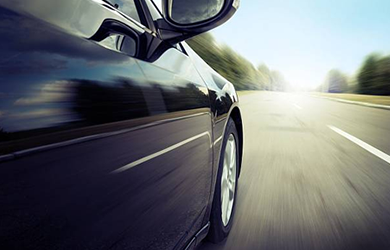
プッシュロータリ曲げ加工技術
ハイテン材の小R、複合R曲げが可能なパイプの曲げ加工技術です。
プレッシャーダイにより、素管を周方向に絞りながら曲げる新しい曲げ加工法で、高強度鋼管の効率的な小R、複合R曲げが可能となり、生産性の向上に寄与します。(JFEスチール(株)、トヨタ自動車(株)、(株)大洋の共同開発)
特 長
- ハイテン材の小R曲げ加工が可能です。(図1)
- 曲げ金型を複合R形状とすることで、直線部を含んだ複合R曲げ加工を1工程で実施することが可能です。(図2:従来の回転引き曲げ加工法では不可)
- 従来の回転引き曲げで必要とされた芯金およびしわ押さえ工具(図2)なしで、薄肉鋼管の小R曲げ加工が可能です。(図1)
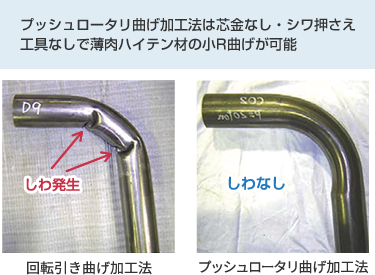
プッシュロータリ曲げ加工後サンプルの比較
材料:780MPa級、φ70mm×t2.6mm、曲げ半径比:R/D=2.0
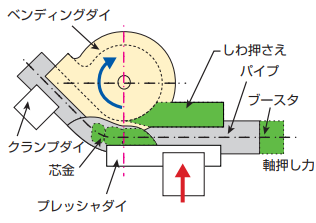
技術のポイント
- プレッシャダイのパイプ長手方向における加圧位置を曲げ金型の回転軸芯位置に一致させるように配置します。(図3)
→プレッシャダイに大きな押し付け力を負荷することが可能 - プレッシャダイによる押し付け力でパイプを周方向に絞りながら曲げ加工を実施します。(図3右)
→芯金・しわ押さえ工具無しで、曲げ内側のしわを抑制可能 - プレッシャダイ圧力制御により、プレッシャダイが金型のR形状に応じて前進・後退が可能です。
→直線部を含んだ複合R形状を1工程での曲げ加工が可能
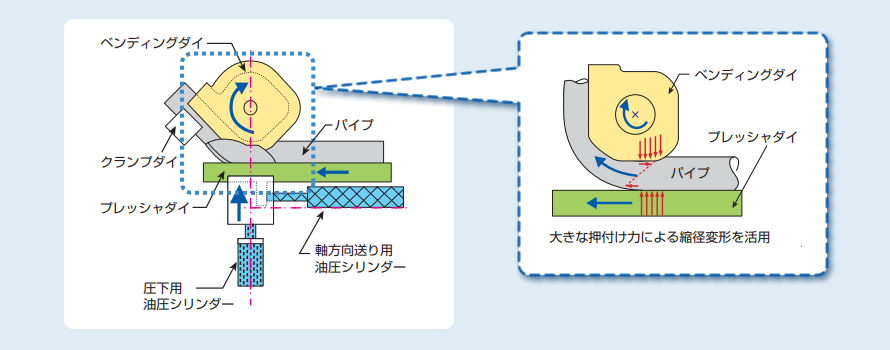
適用可能な自動車部品
- 自動車用構造部材
ロアアーム、サスペンションサブフレームメンバー、トレーリングアーム等の自動車足回り部材の曲げ加工工程に好適。 - 自動車のサスペンション部品の曲げ加工に採用中(図4, 図5)
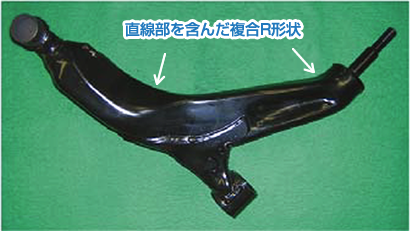
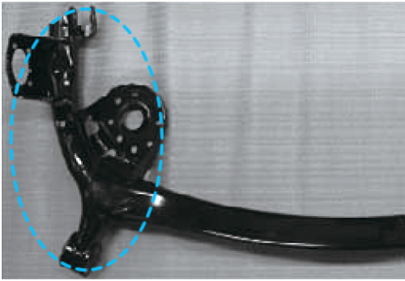
耐遅れ破壊特性 評価技術
使用環境に応じた、自動車向け超ハイテン鋼の耐遅れ破壊特性を評価する実験技術を御提供します。
自動車用部材の超ハイテン化(TS>980MPa)に伴い、材料の選定に当たり、耐遅れ破壊特性がクローズアップされるようになりました。そのため、使用環境(応力・侵入する水素量等)に応じた、耐遅れ破壊特性評価が必要です。
JFEスチールでは、耐遅れ破壊特性を評価する実験技術&ラボ設備を有し、想定される環境を模擬した耐遅れ破壊特性評価を実施します。
特 長
- 想定されうる鋼材の使用環境に応じた、耐遅れ破壊特性を評価できます。
- 遅れ破壊の影響因子として重要な「(拡散性)水素量」と「切欠き(応力集中)」の効果を、それぞれ独立に制御して、鋼材の耐遅れ破壊特性を評価します。
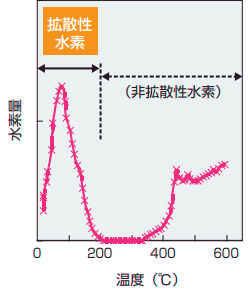
(昇温脱離式ガスクロで測定)
技術のポイント
(拡散性)水素と、切欠きの効果を、模擬する使用環境に応じて、それぞれ、独立 に制御します。
- 水素チャージ:電気化学的手法で実施 ⇒ 拡散性水素量をコントロール可
もしくは、酸等の薬液浸漬によって実施 - 切欠き効果 :機械的な切欠きを付与 ⇒ 応力集中係数をコントロール可
評価手法(例)
高強度で使われる自動車用材料(トーションビーム、スタビライザー等)の耐遅れ破壊特性評価に適用可能です。
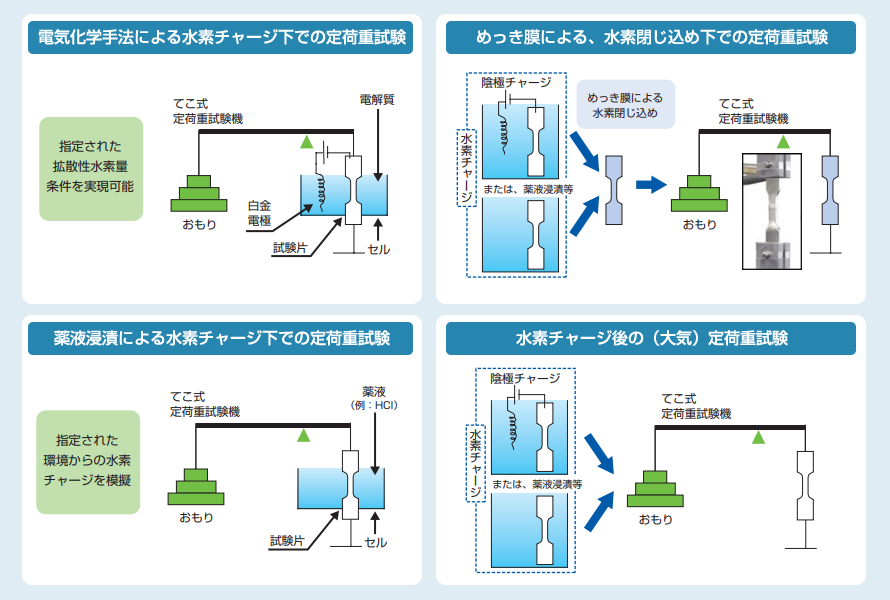